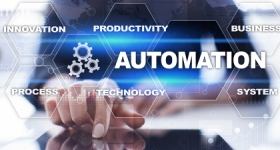
What does Open Automation Software do? The question is more what it doesn’t do. When it comes to industry automation, the OAS product lines allow for complete customization of a system that provides an easy to use OAS toolkit for automated data collection in everything from nuclear submarines to automotive factories and machine shops.
Why OAS and not some other software? The reason is that when it comes to SCADA, IoT, and HMI technology, Open Automation is built around the principle beliefs that software should not only be easy to implement and cost effective but should extend far beyond the control room.
Here is a beginners guide to some of the uses of Open Access Automation Software, and how it works with different components.
Robots and Sensors
The heart of any automation system involves two things: sensors and robots. Sensors gather data about either the production line, a power network, or even the operations of a nuclear submarine’s motors. Not only is the data gathered, but it is processed and analyzed, allowing robots to take action or alert human operators, whichever is most appropriate for the situation.
The term robot can apply to anything from automated arms that pick up and hold parts for machining to an automated system that opens and closes valves in a water distribution system or machine cooling system. From the most complex to the simplest IoT component, robots are found everywhere.
Operator Interfaces
The other key component of any open automation software system is the operator interface. This is simply the method by which the human operator interacts with the machines. Typically this can vary from a production worker orienting certain parts correctly in a drawer so the robot can pick them up for machining, to a warning on a mobile device that a certain part of the production line needs attention or that a certain process is outside of specifications.
Essentially this is for when changes are beyond the scope of what the automated system can do, or in cases where the system needs input from a human operator. The application you are using the software for will determine what this interface looks like. the point is that the interface in this case is open source, and customizable to meet the individual needs of your business and your production line.
Repeatable Positioning and Process
How does automation work so well in many industries? The process being automated consists of one or several repeatable steps. For example, making a car door handle is a repeating process. It is done the same way over and over with no variations. The automation of this process is simple because every step is predictable: a certain amount of metal or plastic is heated to liquid form, poured into a mold in a repeating amount, cooled for a certain amount of time to ensure it is solid, removed from the mold, and sent down the production line.
Each positioning of the mold and components is predictable and repeatable, and overall the entire process is repeatable as well. The cycle could conceivably go on as long as needed with no human interface or input at all. In this case an operator might be alerted if temperatures go too high or too low, the cooling system stops working, or the molds need to be replaced.
The question to ask is what your process looks like? How can you customize the human interface with repeatable positioning and process to make your system work flawlessly?
Workholding
In production, especially the machining of parts, the way the objects being worked on will be held is of utmost importance. A hydraulic or pneumatic system is the most common, and each has its advantages or disadvantages, automated or not. However, the automation of these processes requires that tools and holding devices be modified for robotic control.
Why is this vital? Because too much or too little pressure, the wrong type of vise, and two or more types of holding devices that don’t work well together can damage the process and be an expensive lesson.
These considerations are vital when using an open access software. The customization available should be explored as broadly as possible, and workholding methods and tools modified as necessary.
Remote Access
One of the key features of Open Access Automation Software is the ability to control things remotely, to access data, run reports, and act on information far from the site of your production or process. Human oversight and even interference when needed can happen nearly anywhere there is a reliable internet connection.
This opens up some amazing possibilities. No matter what your process looks like or the kind of data you are acting on, managers and others can be located far from the factory floor, and still easily access data and reports when upper management has questions or concerns. This system is designed to make production as easy as possible while at the same time maintaining the ability to customize and interact in every way necessary.
Open Access Automation Software is the answer for any number of businesses and processes. Understanding the basics of how each system works will help you make the right decision for your process and your team.